Before purchasing carbide end mills, ensure you know your needs. The best choice for your job depends on the material you are cutting and your production rate. To ensure a smooth operation, use carbide end mills with the correct feed rates and speeds. Also, use coolant or compressed air to prevent the buildup of chips. Lastly, consider the length of your end mill.

Coatings
When buying carbide end mills, it is important to consider the coating. This coating can increase the tool's durability and cutting speed. It also protects against built-up edges resulting from materials sticking to the cutting edge. This can lead to chip separation.
There are several common coatings that are available. Some are for general purposes, some are specialized for specific purposes, and others are available only for a single material. The most common types are square and flat. These types excel at various milling operations, including profiling, slotting, side and face milling, plunging, and grooving. In addition, Flat End Mills are ideally suited for roughing applications.
Another important factor is the end mill's diameter. Different end mills are made with different diameters and offsets. When buying carbide end mills, always make sure that you choose the right one for your needs. If you're using it for cutting steel, you'll want to look for a carbide end mill with an HRC55 hardness.
Geometry
When purchasing carbide end mills, you'll want to pay close attention to geometry. While endmills may all look alike, their geometry determines how well they cut. The exact degree of geometry varies for different grades of carbide. Still, it's important to note that each one performs slightly differently, depending on the material, feed rate, and other factors.
Carbide end mills can be expensive, but they are an essential tool for almost any successful industrial milling job. They can be used for roughing, finishing, and material-specific operations. The right carbide end mill can save you thousands of dollars in the long run.
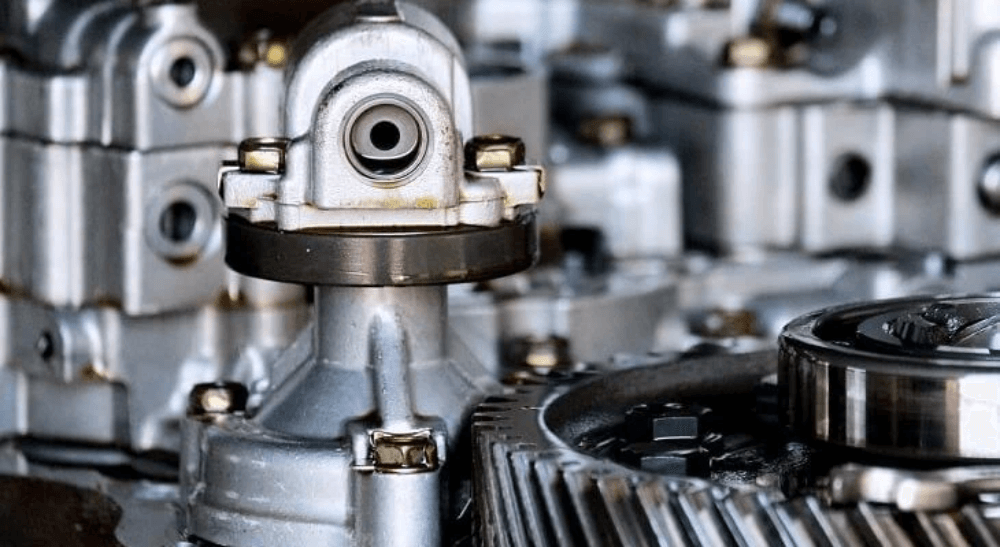
Rpm
When buying carbide end mills, there are a few things to remember. For example, it is important to understand the importance of feeds and RPMs for specific operations. Using an end mill speed table, you can also find the right speed and feeds.
Carbide burrs come in many different shapes and sizes. Choose the right burr for the job at hand. Depending on the materials you're cutting, you may want to choose a burr with multiple cutting faces. For example, a diamond-cut burr will produce a very different profile than a single-cut burr.
While carbide end mills are excellent for hard-to-cut materials, they are unsuitable for all applications. Carbide end mills can be subject to sub-optimal RPMs, reducing overall effectiveness and tool life. In addition, they are more expensive than their HSS counterparts.
If you're on a tight budget, investing in an HSS end mill may be better. HSS end mills are more forgiving regarding sub-optimal RPMs, don't require rigid setups, and are significantly less expensive than their carbide counterparts.
Feed rate
When buying carbide end mills, it's essential to consider the feed rate, which is the rate at which the end mill cuts the material. High feed rates can result in a chip that is difficult to break, and the high rate can lead to end mill breakage. Feed rate is also a factor in determining the depth of cut. Check out this site to know more about carbide end mill feeds.
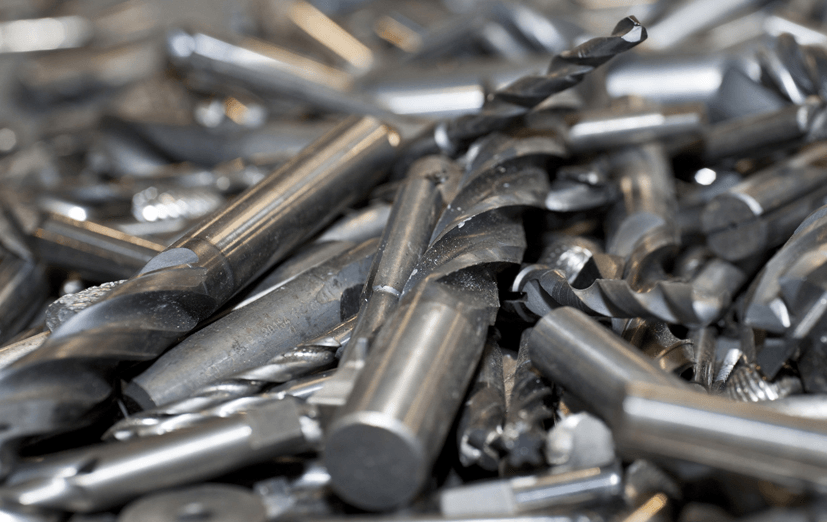
Hardness
Another consideration is hardness. Hardness determines the amount of wear the tool will have. Higher hardness means a longer tool life. However, carbide end mills are less resilient to wear than high-speed steel.
Length of cut
One of the most important factors to consider when buying carbide end mills is the length of the cut. This measurement reflects the maximum length of the cutting edge during the operation. The shortest length is the optimal choice, as this minimizes overhang and reduces chatter. Longer lengths are beneficial for applications that require deep cuts.
Different materials and applications require different lengths of cut. Using the proper length of cut can help you get the best results and cut the fastest. Choosing a carbide end mill with the appropriate geometry is also crucial.